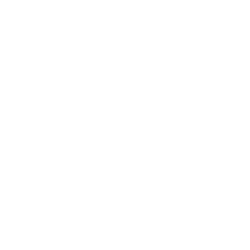
SMITHFIELD GARDENS ASSISTED LIVING COMMUNITY
Smithfield Gardens, a 56-unit affordable assisted-living facility in Seymour, CT, installed a Combined Heat and Power (CHP) system in the boiler room during the construction phase of the building.
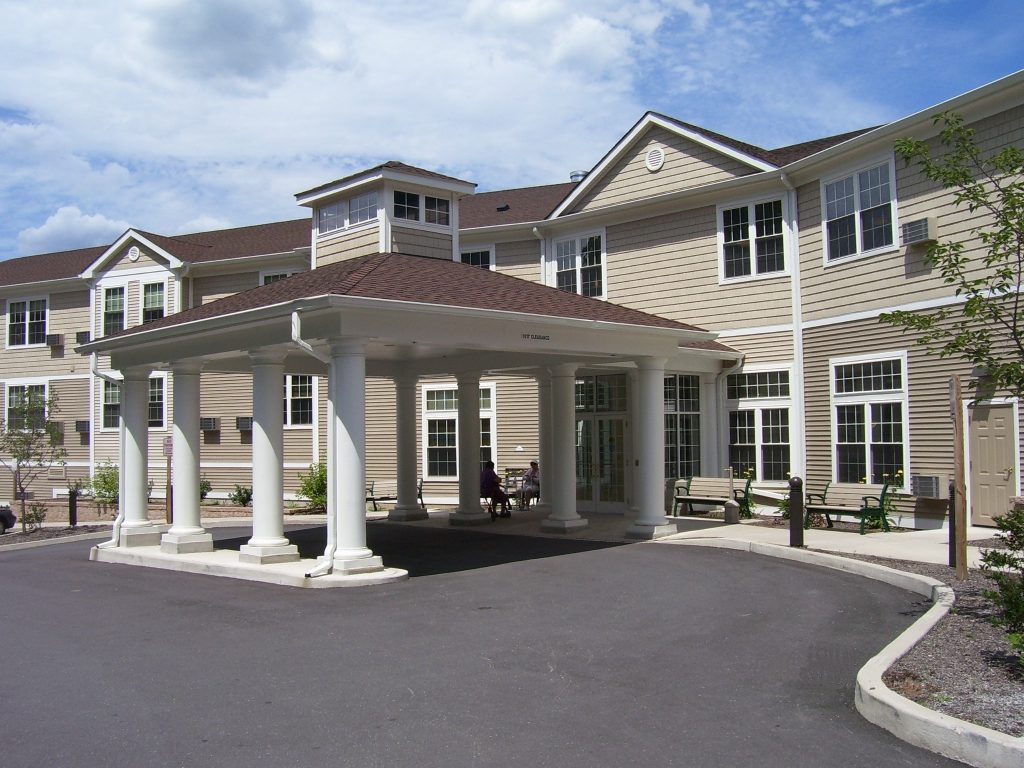
Quick Facts
- LOCATION: Seymour, Connecticut
- FUEL: Natural Gas
- MAX CAPACITY: 75 KW
- POLLUTION CONTROL: Non-Selective 3-way Catalytic Reduction system
- ENVIRONMENTAL BENEFITS: 74% NOx reduction, 32% CO2 reduction
- AVERAGE CAPACITY FACTOR: 90 %
- IN OPERATION SINCE: November 2006
- EQUIPMENT: 75kW Aegen 75-LE cogenerator, American Yazaki absorption chiller, Baltimore Air Coil cooling tower
- USE OF ELECTRICAL ENERGY: Displaces building loads previously supplied by the local utility
Site Description
Smithfield Gardens, a 56-unit affordable assisted-living facility in Seymour, CT, installed a Combined Heat and Power (CHP) system in the boiler room during the construction phase of the building. The energy-saving cogeneration system consists of a 75 kW Aegen 75LE CHP module, supplied and installed by Dalkia Aegis, of Holyoke, MA. The highly efficient Aegen 75LE module employs an oil cooler, engine jacket, exhaust gas manifolds and heat exchangers, in order to recover otherwise wasted heat.
Reasons for Installing CHP
The Smithfield Gardens Assisted Living complex was developed by the Seymour Housing Authority. The housing authority had been pleased with the cost-savings it experienced with a similar CHP system, engineered and installed by Dalkia Aegis, EDF Group, at another one of its facilities located next door at Callahan House. Anxious to proactively reduce their operating expenses at Smithfield Gardens as well, they contacted Dalkia Aegis about the potential for a CHP system in that facility. The energy analysis revealed that Smithfield Gardens could save 22% on its annual energy costs by employing a CHP system. Dalkia Aegis remotely monitors Smithfield’s CHP system to ensure high runtimes and efficiency. In addition, Smithfield has contracted with Dalkia Aegis for the comprehensive maintenance of their system.
The 500,000 kWh of electricity annually generated by the system supplies 56% of the total building demand, and offsets loads typically supplied by the local utility. The recovered heat from the engine is used as the source of energy to drive the absorption air-conditioning system in the summer, along with winter space heating and domestic hot water on a year round basis. The CHP system supplies 54% of the building’s thermal requirements. Natural gas boilers provide peak heating energy when required. The water-fired absorption chiller provides 10 tons of cooling capacity, thus offsetting the expensive to operate electric chillers. Absorption cooling relies on heat instead of electricity, in order to operate.
Lessons to Share
Absorption Chillers add to summer thermal load thus improving the payback on a CHP system.
Service contracts are important to maintain CHP systems to maximize energy savings.
Housing authorities are sensitive to energy costs and are forward-thinking about energy technology.